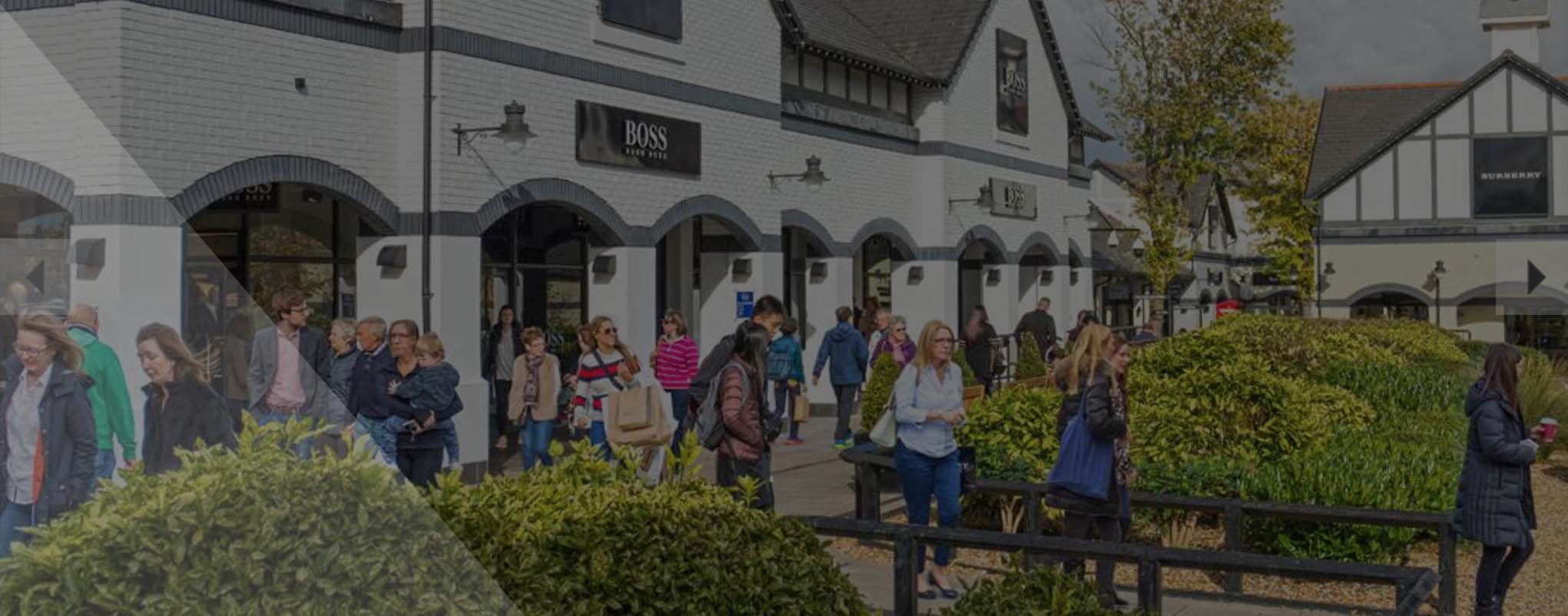
McArthurGlen
M&E Asset and Fabric PPM Surveys
Challenge
McArthurGlen initially approached Sircle (or Topscan as we were then known) in 2018 to undertake M&E asset and fabric PPM surveys across their portfolio of UK and European sites. The objective was to allow them to proactively manage and correctly maintain all their building fabric and M&E assets and reduce cost by not over maintaining. Creating long-term plans for replacement assets was another aim, which included sighting when significant investment was likely required for assets, or fabric, expected to come to the end of their lives.
Solution
We sat with the client to fully understand the reason behind the surveys, the areas and assets in scope and put together a detailed brief. This would guarantee the client got the information they required and enable our in-house surveying team to develop a bespoke survey scope.
To ensure everything was captured and presented correctly, separate scopes were put in place for the M&E asset and building fabric planned preventative maintenance (PPM) surveys. Sircle were able to use their experience to identify a clear methodology to ensure the successful delivery of this project. The first stage was to review the existing building asset data available, allowing us to identify the key building assets coming towards the end of their lifecycle period. We were then able to upload this existing data through our data capture software to ensure this could be checked on-site and updated as required and collect any new building asset lifecycle data.
Our data structure for this project aligned with SFG20 & NRM3. This provided a standard set of measurement rules for estimating, cost planning, procurement and whole-life costing for construction projects and replacement, making our lifecycle reporting accurate, aligning with a set of recognised industry standards.
Outcome
Upon completing the surveys, we presented the data in the agreed manner, allowing for creation of a PPM schedule. This ensured labour loading could easily be calculated and reviewed.
The reports included details of each asset as well as summary cost by year, by element and condition grade and other further detailed information. This helps them plan, budget and forecast over a period of up to 25 years.
Pleased with the surveys we initially completed for them, the client asked us to return to their Cheshire Oaks site in 2021 to refresh the existing information that had become outdated, i.e. several new buildings and refurbishments weren’t reflected.
We also highlighted several larger building assets that required attention in the next few years, allowing our client sufficient time to plan and budget without the unexpected reactive costs.
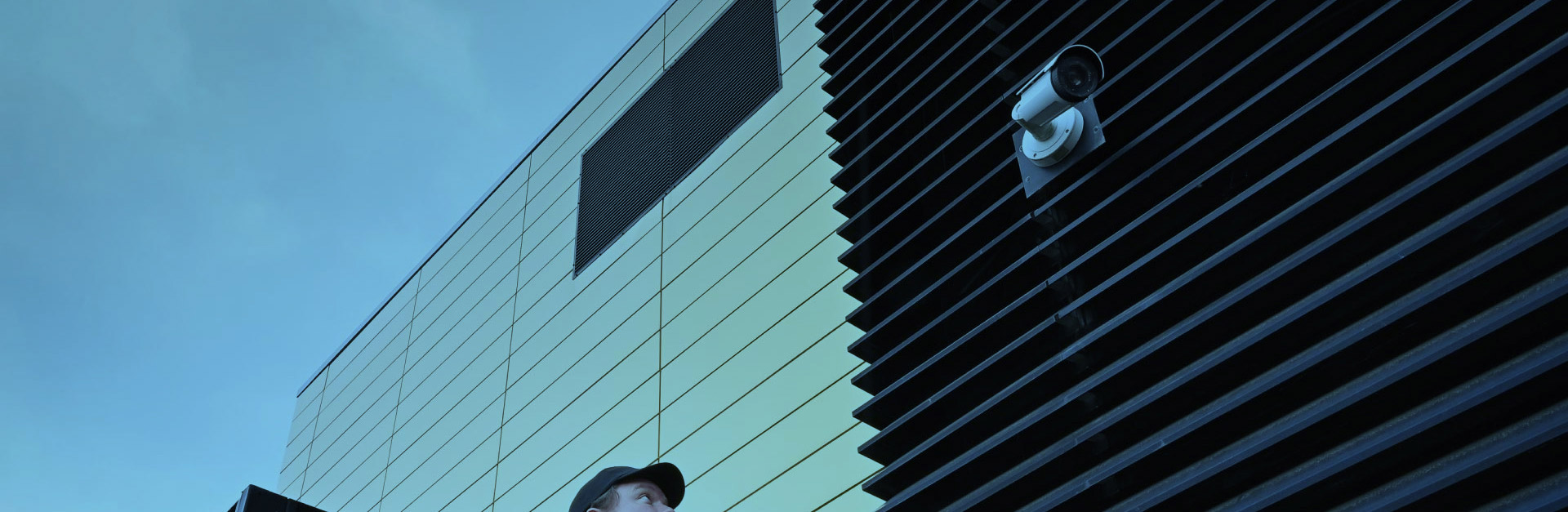